Top-tier plastic extrusion solutions for manufacturers
Top-tier plastic extrusion solutions for manufacturers
Blog Article
Recognizing the Essentials and Applications of Plastic Extrusion in Modern Production
In the world of modern-day manufacturing, the strategy of plastic extrusion plays an instrumental role - plastic extrusion. This complex process, including the melting and shaping of plastic via specialized passes away, is leveraged across numerous markets for the development of varied products. From auto components to consumer items product packaging, the applications are huge, and the capacity for sustainability is similarly impressive. Untangling the fundamentals of this procedure reveals truth adaptability and potential of plastic extrusion.
The Basics of Plastic Extrusion Refine
While it might show up complex, the fundamentals of the plastic extrusion process are based upon reasonably uncomplicated concepts. It is a manufacturing procedure where plastic is thawed and after that shaped right into a constant profile with a die. The raw plastic material, often in the form of pellets, is fed into an extruder. Inside the extruder, the plastic undergoes warmth and pressure, triggering it to thaw. The liquified plastic is after that compelled via a designed opening, recognized as a die, to create a long, continual item. The extruded item is cooled and then reduced to the desired size. The plastic extrusion process is extensively made use of in different markets because of its versatility, performance, and cost-effectiveness.
Different Types of Plastic Extrusion Strategies
Structure upon the standard understanding of the plastic extrusion process, it is essential to check out the different techniques associated with this manufacturing approach. Both main techniques are profile extrusion and sheet extrusion. In profile extrusion, plastic is thawed and created into a continual account, typically made use of to develop pipes, poles, rails, and home window frameworks. In contrast, sheet extrusion creates huge, flat sheets of plastic, which are typically further processed right into items such as food packaging, shower curtains, and cars and truck components. Each technique requires specialized machinery and accurate control over temperature level and stress to ensure the plastic keeps its form throughout air conditioning. Understanding these techniques is essential to using plastic extrusion properly in modern-day production.
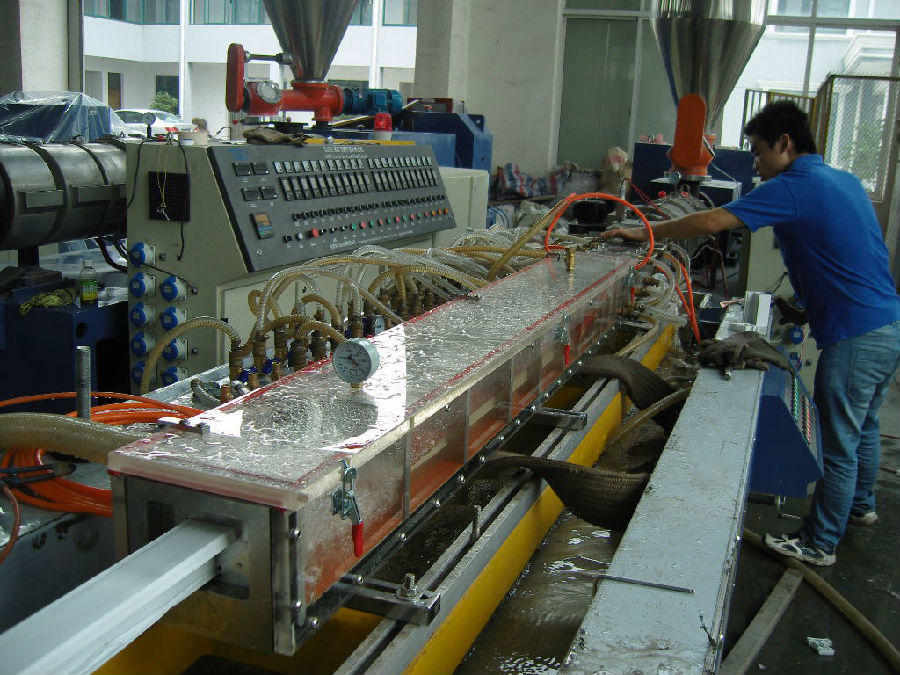
The Duty of Plastic Extrusion in the Automotive Sector
A frustrating bulk of parts in modern lorries are products of the plastic extrusion process. This process has reinvented the vehicle market, transforming it right into a much more reliable, economical, and versatile production market. Plastic extrusion is primarily used in the manufacturing of various auto elements such as bumpers, grills, door panels, and control panel trim. The procedure supplies an attire, constant output, making it possible for makers to generate high-volume get rid of excellent precision and very little waste. The lightness of the extruded plastic components contributes to the general decrease in lorry weight, enhancing gas efficiency. Moreover, the resilience and resistance of these components to warmth, cool, and effect improve the long life of autos. Hence, plastic extrusion plays a pivotal role in automotive production.
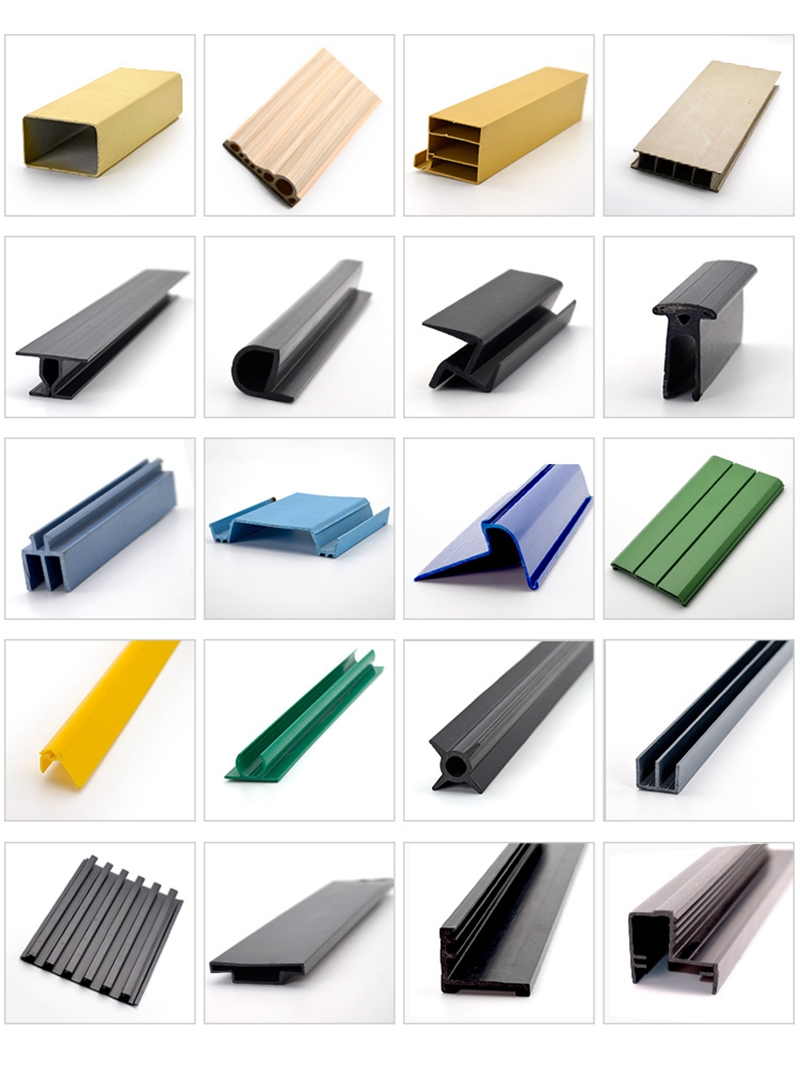
Applications of Plastic Extrusion in Customer Item Production
Past its significant effect on the read this automobile market, plastic extrusion verifies just as reliable in the realm of durable goods manufacturing. This procedure is vital in producing a vast array of items, from food packaging to house devices, toys, and also clinical tools. The flexibility of plastic extrusion allows manufacturers to make and produce complex forms and dimensions with high precision and effectiveness. Furthermore, because of the recyclability of many plastics, extruded parts can be reprocessed, minimizing waste and cost. The versatility, adaptability, and cost-effectiveness of plastic extrusion make it a recommended choice for lots of customer products manufacturers, adding significantly to the market's development redirected here and innovation. The environmental ramifications of this extensive usage call for careful consideration, a topic to be talked about further in the subsequent section.
Ecological Impact and Sustainability in Plastic Extrusion
The prevalent usage of plastic extrusion in making welcomes examination of its eco-friendly effects. Reliable machinery lowers power use, while waste administration systems reuse scrap plastic, reducing raw product needs. Despite look at this now these renovations, better advancement is needed to mitigate the ecological footprint of plastic extrusion.
Verdict
In verdict, plastic extrusion plays an essential role in contemporary manufacturing, specifically in the automotive and consumer goods markets. Understanding the fundamentals of this process is essential to maximizing its applications and benefits.
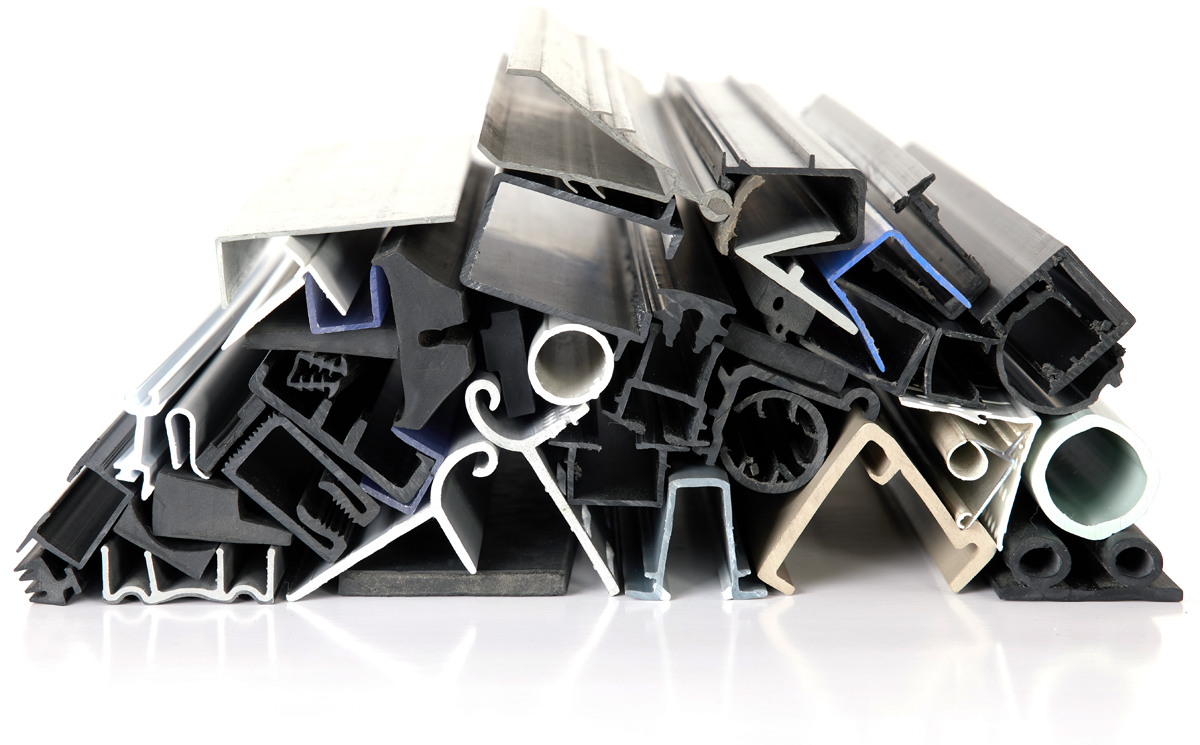
The plastic extrusion process is extensively used in various sectors due to its performance, cost-effectiveness, and convenience.
Building upon the basic understanding of the plastic extrusion process, it is essential to check out the various methods involved in this production technique. plastic extrusion. In contrast, sheet extrusion develops big, flat sheets of plastic, which are commonly more refined into items such as food packaging, shower curtains, and cars and truck components.An overwhelming bulk of components in contemporary cars are items of the plastic extrusion process
Report this page